News | Thought Leadership
Climate Action: Decarbonizing Transportation and Manufacturing
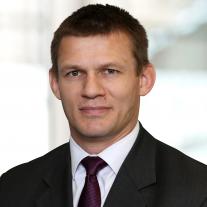
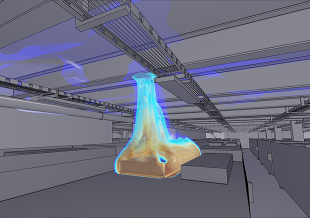
This week in our continuing series showcasing how engineers and scientists can play a key role in addressing the short- and long-term challenges of climate change, our latest blog explores decarbonizing the transportation and manufacturing sectors, which is crucial to tackling climate change, and touches on some of Thornton Tomasetti’s work in supporting this transition. While electrifying transportation is a clear strategy for reducing carbon emissions, manufacturing requires a more nuanced approach.
Decarbonization—reduction of greenhouse gas (GHG) emissions to keep temperature rise below 1.5oC in reference to pre-industrial levels—requires understanding the primary sources of emissions. These are: 1. energy supply and demand, which generates the vast majority of global emissions, and 2. agriculture, forestry and other land use (AFOLU). Energy supply consists of all the primary energy sources used in power generation as well as direct fuel production. This energy is then used by three energy demand sectors: buildings, manufacturing and transportation. The efficiency of each of these sectors provides a useful guide for identification of the optimal decarbonization pathways. In this blog post, we focus on the decarbonization of transportation and manufacturing.
Electrifying Transportation
Energy flow analysis indicates that the overall efficiency of the transportation sector is only ~20%, which correlates with the thermal efficiency of internal combustion engine (ICE). That means that approximately 80% of the energy generated by burning gasoline directly in ICE is rejected as waste heat. At this time, hydrogen fuel cells are being considered as an alternative for long-range uses due to the energy density, with efficiencies as high as 60%. Conversely, electric vehicle (EV) efficiency is typically above 80%. In addition, the efficiency of electricity generation (required to charge the battery), which is currently dominated by fossil fuels, is approximately ~35%, i.e. almost twice the efficiency of ICE. Thus, transport electrification, along with overall efficiency improvements such as light-weighting, are the most efficient decarbonization pathways for this sector. It is useful to add that the efficiency gap between electricity generation and its use by electrified transport (i.e. ~35% vs ~80%) can only be covered by decarbonizing the energy supply, which is a separate topic.
Enabling this transition requires overcoming multiple new engineering challenges, such as risk of thermal runaway in li-ion batteries, which can lead to fire, explosion and toxic gas release. This is an important consideration for large parking garages and other structures housing EVs. We are currently working on ensuring safe operation of multiple parking garages, bus depots and other facilities housing large li-ion batteries as well as hydrogen.
Multipronged Approach to Manufacturing
Performing a similar energy flow analysis for manufacturing, with a focus on carbon-integral processes and high-energy manufacturing campuses, indicates that electrification is not necessarily the optimal decarbonization pathway for industry. This is mostly because the overall efficiency of manufacturing is ~50%, which is significantly higher than efficiency of electricity production (i.e. ~35%, with the current hydrocarbon-dominated fuel make up). This shows clearly that electrification of manufacturing, even if it were possible, would actually result in increasing the emissions, at least until the energy supply transition towards renewables and nuclear sources is complete. Thus, the order of decarbonization of the energy supply and demand plays a key role in identifying the most effective transition pathways, and energy supply decarbonization should, ideally, come first.
Another important challenge relates to the manufacturing sector’s reliance on carbon-based feedstock. Cement and steel industries are examples of hard-to-abate sectors. Cement clinker is produced by calcining limestone, or calcium carbonate (CaCO3), which requires heating the kiln to a high temperature (usually achieved by burning fossil fuels). This produces a calcium-based clinker product and CO2. Thus, even if all fuels were replaced with clean electricity or renewable fuels (e.g. hydrogen), only ~40% of the sector’s total GHG emissions would be abated. The remaining 60% is directly related to the underlying chemistry of the calcination process. This points to a need for new technologies for manufacturing everyday materials, which will likely require decades of research and innovation. In the meantime, there are other methods and technologies, such as carbon capture and storage (CCS), that can be applied to decarbonize, albeit partially, the manufacturing sector. In some cases, full replacement of fossil fuels with green hydrogen can also provide a deep decarbonization pathway.
The other area that is hard to decarbonize is large manufacturing campuses, like car and chip manufacturers. They tend to have many small emissions points that, once aggregated, have high GHG impact. They also need highly dependable backup power, which traditionally comes from diesel generators. The primary method for decarbonizing these manufacturing campuses is to electrify all of the minor energy users. This is similar to decarbonization and electrification evaluations done for the building sector; any energy efficiency savings can also have a positive impact on the overall carbon footprint. However, considerations for energy resiliency must take precedence in this evaluation, ensuring there is reliable backup power available to remain online. This journey may also involve replacing diesel generators used as emergency power backup with batteries.
As in the case of transportation, our firm is actively supporting this transition by engaging with steel and cement manufacturers to develop new processes allowing reduction of both embodied and operational carbon. We are also supporting the transition by engaging our manufacturing and industrial clients early and helping them optimize their decarbonization pathway.
Climate change is one of the biggest challenges facing our society. And because it affects everyone, it demands our creativity, passion and collaboration to build a better, more enduring world. See how Thornton Tomasetti is one of the only firms with the expertise to help you think holistically about a range of steps to address climate change.